Intelligent Equipment
Onward Rise
- Home
- Intelligent Equipment
Management Thinking + Technology Integration
Enhancing Overall Corporate Operational Value
Address Your Pain Points
Management
Pursuit Goals:
Zero Accidents, Zero Losses, Zero Failures, Zero Defects
Technology
Victor Taichung's Intelligent Assembly Line + Processing Line
Big Data Collection / Visualization / Diagnostic System / Health Check System / App Development
Network Layer (IoT)
Perception Layer (Sensors, Image Vision, etc.)
Equipment Layer (Intelligent Machine Tools, Intelligent Robots, Peripheral Equipment, etc.)
IOT IOT IOT IOT IOT
Purpose of Victor Taichung Development V4.0
Begin with the end in mind, creating value for customers
Provide intelligent automation system technology integration
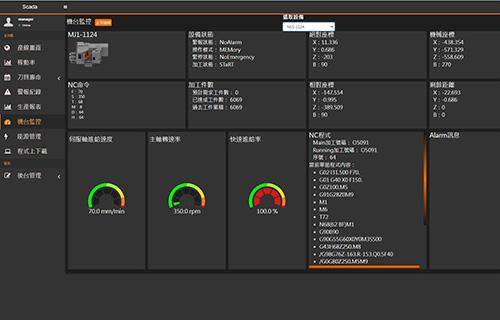
01
Equipment Status Monitoring/Process Management
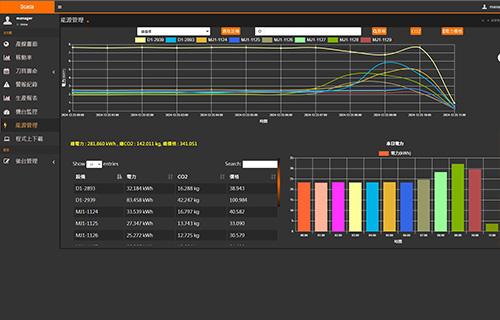
02
Health Check and Predictive Maintenance Services & Power Monitoring
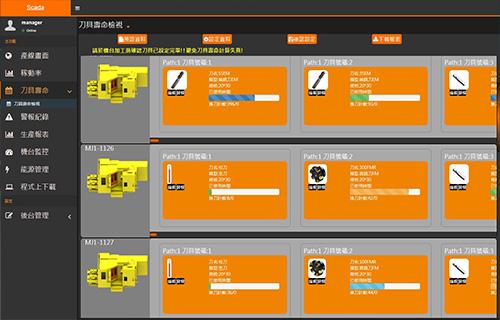
03
Machining Program/Tool Management/Tool Life Management
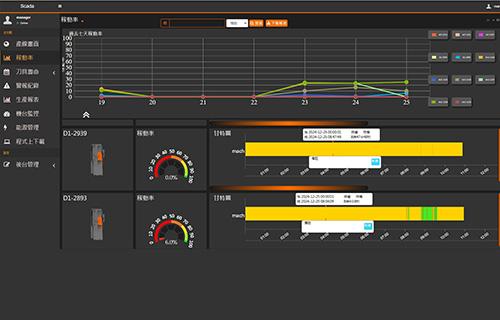
04
Operation Management, Machining Performance, and Fault History Records
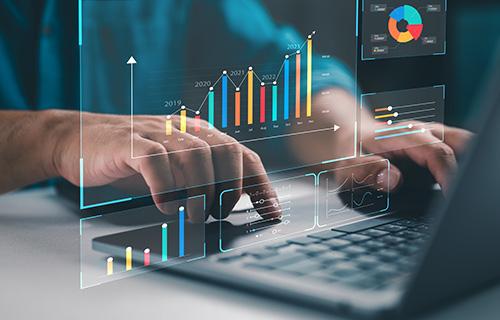
05
Big Data Collection and Analysis
- Automatic Data Collection, providing real-time production data needed by production managers at all levels.
- Processing users can accurately monitor machine status through real-time full-plant monitoring, utilization rate management functions, equipment alarm history analysis, and complete data records.
- Combining OEE (Overall Equipment Efficiency) allows for true production progress and output tracking.
- Implementing Performance Management, using real-time equipment health status inquiry systems, machine abnormal record/report systems, to accurately grasp machine health status.
- Avoiding resource waste caused by downtime, improving production efficiency, and continuously improving management goals.
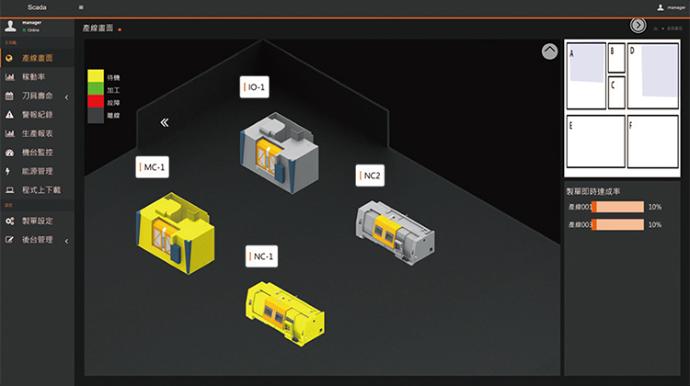
Main Screen
- Real-time machine status and production information collection.
- Overall equipment efficiency (OEE).
- Tool life inspection.
- Alarm analysis.
- Energy management (optional).
- Machine program upload/download.
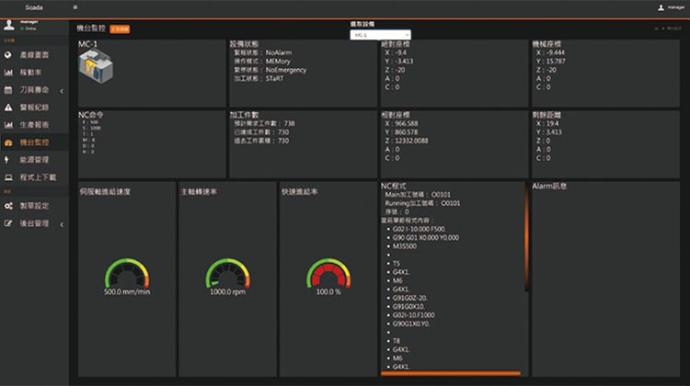
Real-Time Machine Status Monitoring
- Real-time information display of production line machines.
- Real-time data display of individual machines.
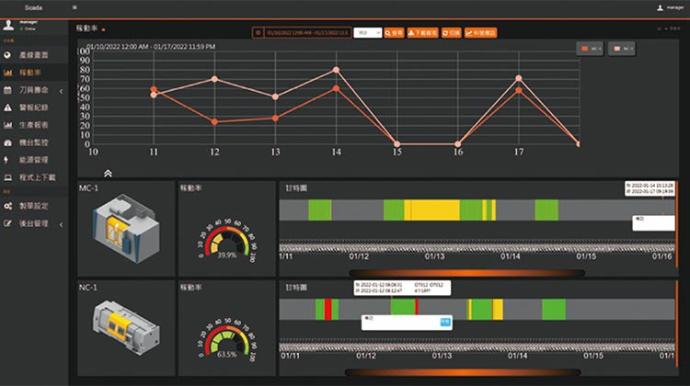
Overall Equipment Efficiency (OEE)
- Real-time utilization rate analysis.
- 即時加工狀態分析。
- Real-time production data analysis.
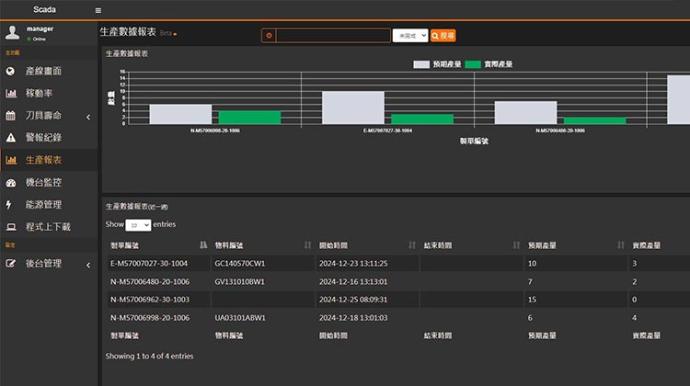
Production Information Collection (Production Reports)
- Production data statistics.
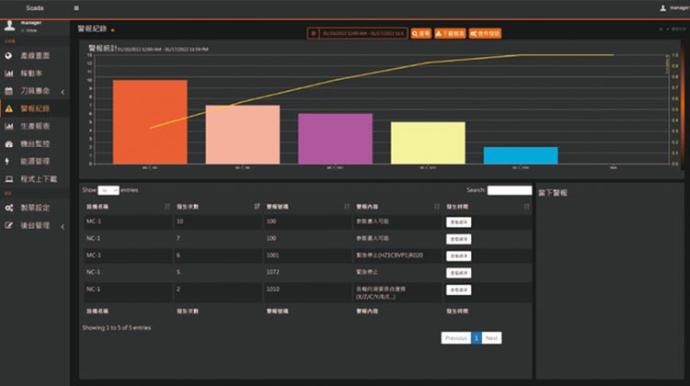
Alarm Analysis
- Display of abnormal occurrence data for production line machines, abnormal record analysis/comparison with past data.

Energy Management (Optional)
- Machine power inspection/power consumption analysis.
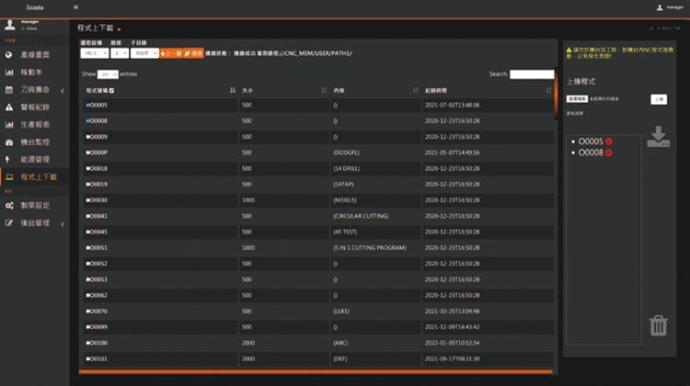
Machine Program Upload/Download
- Program transmission (operated on the PC side).
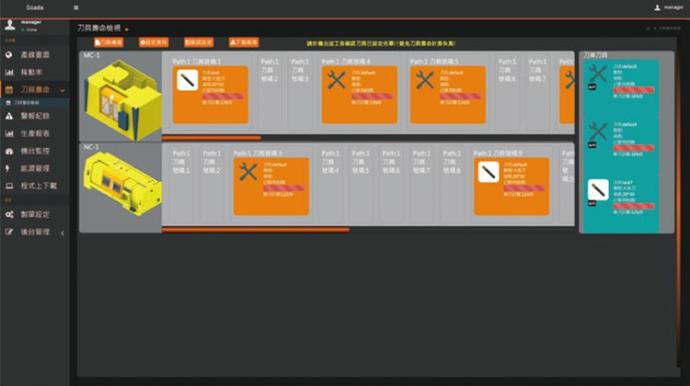
Tool Life Inspection
- Inspection of tool data used by production line machines, and statistics of the usage ratio of each tool, tool usage analysis/expired tool alarms.
- Analysis of all tool usage ratios for production line machines.
- Display of the number of tools with a usage ratio exceeding the warning ratio.
- Inspection of average usage rate.
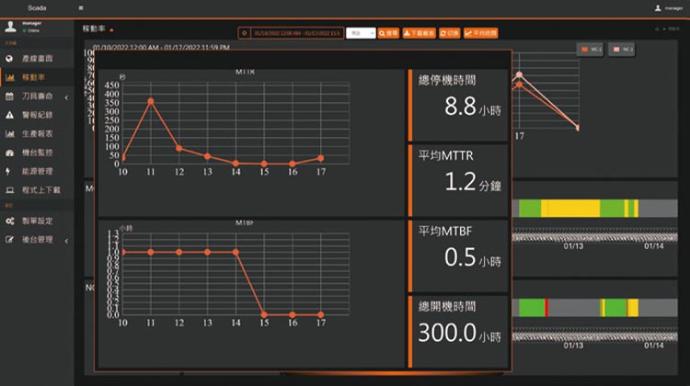
MTFB/MTTR Indicators
- MTTR (Mean Time to Repair): The average repair time for a repairable product, from the occurrence of the fault to the completion of the repair. The shorter the MTTR, the better the ease of recovery.
- MTBF (Mean Time Between Failures): The average time from the start of work under specified working conditions to the occurrence of the first failure.
- The longer the MTBF, the higher the reliability and the stronger the ability to work correctly.
3D Diagram (4.1~4.4)
- Compared to manual operations, the robotic arm can reduce the mold change time from 24 minutes to 2 minutes, improving efficiency by 11 times.
- Capable of producing small batches with various specifications, currently able to produce over 155 types of workpieces.
- Both scheduling software and SCADA software are self-developed by the company, meeting visualization and customization needs.
- Automatic chuck exchange technology connected to the storage system can reduce the number of molds and fixtures, lowering costs.
- Equipped with a predictive mechanism to prevent system failures or malfunctions.
V4.1~V4.2 3D Diagrams
Advantages
- Different specifications for each part, small batch and variety
- 3D/2D vision applications
- Automatic lathe chuck exchange applications
- Robotic gripper storage applications
- Self-developed scheduling software and SCADA software, integrating software and hardware
V4.3~V4.4 3D Diagrams
V4.3 Center Machine Automatic Mold Change System
- Production line composed of two robotic arms
- Robots use servo torque guns for screw/pressure plate fastening, as well as fixture and workpiece loading/unloading
- 2D/3D CCD vision applications
V4.4 Guided Installation System and FMS
Advantages
- The FMS (Flexible Manufacturing System) of V4.4 consists of 6 Victor Taichung horizontal machining centers and 80 automated storage systems (for placing workpieces after mold changes), with automatic processing through computer scheduling software.
- Conveyor belts are installed under the floor for centralized handling of iron chips.
- Centralized supply and replenishment of cutting fluid and lubricating oil.
- Single machine oil mist recovery (CanTung brand).
- Oil mist pipes are installed for overall plant system oil mist recovery.
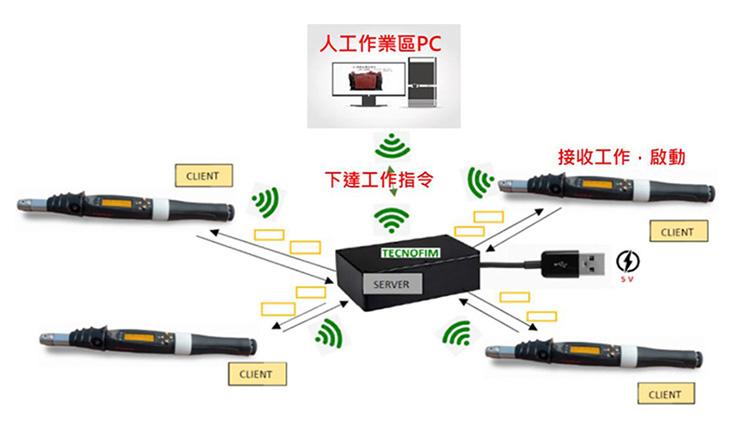
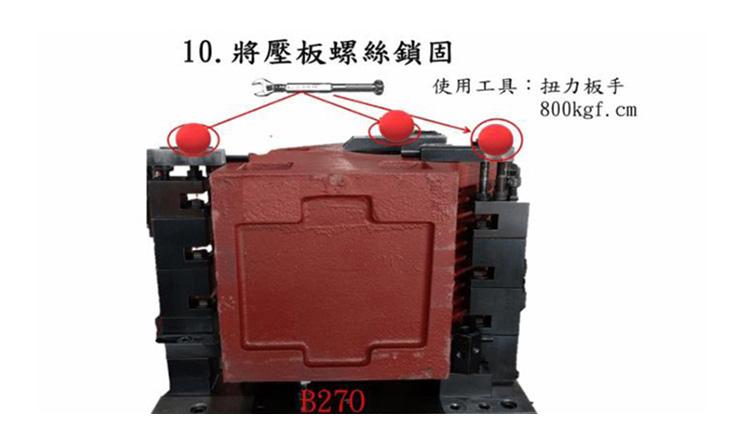
At the loading and unloading stations, the guided installation system is used for large and complex workpieces. Personnel complete correct mold preparation through guided screens and wireless torque setting and confirmation signal exchange.
- Application of Wireless Torque Wrench
Efficiency Different Specifications for Each Part, Optimized Processing Efficiency Mechanism - Single Piece Processing